Dave Darby of Stroud Commons and Lowimpact.org talks with Rosie Bristow and Nick Evans of Fantasy Fibre Mill, working to resurrect the flax / linen industry in the UK, as a commons.
Dave: you contacted us to talk about commons ideas and the possibility of building a textile commons. I think that’s very important. Supply chains for textiles are so huge, and the industry is so exploitative and damaging to the biosphere in so many ways. What attracted you to the commons approach?
Rosie: I’ve worked a lot with Makerspaces, which was a big inspiration for me – especially the open source technology. They had 3D printers and arduinos – technology that used open source software or open source hardware. They share their knowledge online – a knowledge commons, rather than patenting their ideas. I’m keen to keep everything open source, and share the tech with as many people as possible. Farm Hack was another inspiration, which shares designs for farm equipment. Nick’s more familiar with the software.
Nick: I was very familiar with the concept of open source, but the concept has moved away from where it started – freely sharing code. I came late to the commons. We were doing something for a long time, and I didn’t realise that it was actually commoning that we were trying to do. We want to get on the commons bandwagon. I was confused by the term commons at first. I thought it applied to resources like land etc. But the flax industry isn’t there yet. But I’m interested in commonING – to develop the flax industry as a commons – ways of organising ourselves that are not driven by market or state.
Dave: I could interview you about the flax industry, and the work you’re doing to revive it. I could then show the recording and the transcript to commons specialists, give them time to think about it, then interview them about how the sector might be brought into the commons. I can then show you the transcript and recording of that, after which I can bring you together for a joint discussion, to see how we might go forward. That might work for all sectors, actually.
Rosie: that sounds like a great approach. We can listen and digest each others’ thoughts before coming together for a chat.
Dave: the task you’ve given yourself is massive, isn’t it? You have to resurrect the old flax/linen industry, but in a small-scale, decentralised way. That could include growers, processing, spinning, weaving, dyeing, distribution and retail – a huge network with a lot of planning. But very exciting.
Rosie: yes, it started when I wondered if I could grow my own clothes. I was volunteering on an organic farm during lockdown. I was fascinated by all the processes. I thought about the textile equivalent. I read a great book – Fibershed, by Rebecca Burgess, in which she tries to build a wardrobe from within a 150-mile radius from her house in California. She built a network of growers, processors etc. that became the first Fibreshed. I wanted to do the same in the UK. But there isn’t any processing equipment in the UK. I spoke with a lot of farmers who’d love to grow flax, and a lot of people in the fashion world interested in locally-produced, regenerative fibres. So I set off on a journey to try to build machines from scratch, at an appropriate scale. Nick volunteered at our first every flax harvest, and he started building machines.
Dave: so you’ve already built machines?
Nick: yes, we met in a flax field in Essex in 2021. Rosie had started her masters, and had started building hand prototypes of the machines. She pointed me towards Studio Hilo, a Berlin-based textile design studio, who’d designed a table-top spinning machine. It was small, arduinio-driven (open source hardware – a tiny computer used for powering 3D printers / home and hobby automation projects). It was great, but only did a tiny part of the process. If we want to create a micro-mill to do everything from fibre to yarn, we need to build a lot more machines. We looked at a lot of old textbooks of historical flax-processing machinery. About a year ago, someone from Herriot-Watt university encouraged Rosie to turn this into a business, and we applied for grants from Innovate UK, and we were successful last year, which allowed us to build a mill in East Lothian, Scotland. We’re building prototype machines and we’ve brought some engineering specialists on board.
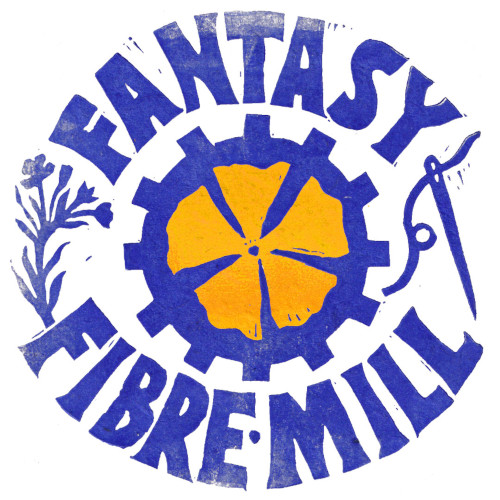
Dave: so you have a mill already?
Nick: yes – so flax processing 101: you have flax straw. You need to break up the outer woody core. We have a breaker machine to do that – with big rollers to crush it. Then we put it through a machine called a scutcher – wooden blades that spin and bash against the fibres, to further remove the outer woody bits. Then it goes through a series of combs, and you get flax fibres that look a bit like hair. These machines are now working, in our mill in Scotland. We can extract fibre from flax. We need to fine-tune them to make them more efficient.
Dave: can I just ask – why flax? Why not hemp, or nettles etc?
Rosie: all 3 you mentioned are bast fibres – ie the fibre is in the stalk. The process is similar for all 3. We’re hoping the machinery can be modified for hemp (it would have to be bigger, because hemp is bigger). But flax is the easiest to farm. You can harvest nettles from the wild, but they’re not really farmed, plus they’re more difficult to process, because they have more nodules on the stems. And hemp is great, but it needs extra licences, and there’s a huge amount of paperwork you have to go through for the government.
Dave: why is that? What’s the problem with hemp?
Rosie: it’s because it’s closely related to cannabis.
Dave: but you can’t smoke it?
Rosie: no – it’s really silly. It doesn’t make any sense. It’s not controlled by DEFRA, but by the Dept for firearms and drugs. You have to apply to that dept. for a special licence. And there are rules – for example, it can’t be seen by the public, so you can’t grow it next to a road, or on land with a public footpath.
Nick: hemp is trendy at the moment, but it is more difficult to process, because it’s bigger and tougher than flax.
Rosie: if it were easier to grow hemp, we’d probably be doing both, just to see how it goes.
Dave: what successes have you had so far? Does all your machinery work well enough?
Rosie: the first 2 machines are working well. We’ve got them all hooked up to their motors. We’re now at the stage of fine-tuning the next 2 machines, including spinning the fibre into a yarn. We’ve got prototypes of those machines, but we have to work out how to get the best out of them, to make good-quality yarn.
Dave: so you haven’t made any linen yet?
Rosie: not yet, but soon, hopefully. I’ve made some myself by hand-processing and spinning and handweaving, but not yet from our machines.
Dave: just moving away from process for a moment – how does your work link to a sense of place and community? That’s very important in the commons world, obviously.
Nick: one of the reasons we chose flax was because it’s a native fibre to the UK, so to build a UK textile industry, you’d be looking at flax, along with wool and hemp. And the intention of the machinery we have is to enable vertical integration, so that you can have in one farm / place the flax, and all the processing through to yarn that could be made into cloth by local weavers, that could be made into clothes by local designers. So our vision is about enabling place-based processing facilities which then enable community.
Dave: so the whole process could happen in one town?
Rosie: exactly. We’re trying to build farm-scale equipment so that farmers can process their own crop. That’s the idea of open source too. We don’t want to become a massive centralised factory. Our ideal is lots of little hubs all over the place, that can process everybody’s local fibre. We don’t want to replicate the problems of the current system.
Dave: a lot of European fibre plants end up in China to be processed don’t they?
Rosie: yes. About 90%. Only about 10% of French fibre plants remain in France to be processed. We visited organic flax farms in France. They do the first process, but it’s then sent to China for spinning. But they also said that they know of 2 new spinning mills that are opening up in France. So they’re having a big movement towards re-localising their clothing industry. France is ahead of the UK, because although spinning has been done overseas, they still have the growing and processing.
Nick: another thing to do with place. I’m very interested in bridging the rural-urban divide. The first 2 processing machines are best placed on farms, but the second 2 machines are finer and lighter, and could be set in an urban context. That’s a way of connecting a town to its surroundings.
Dave: I live in Stroud, which used to be a textile town. You could almost say that textiles were the real engine of the transition from feudalism to capitalism – first wool and then cotton.
Nick: the story of the Western economy is the story of textiles.
Dave: hopefully it could be instrumental in the transition from capitalism to a commons economy. Fingers crossed. In Stroud we’ve recently launched a land commons group, so we’ll be looking at trying to get our hands on pockets of land around Stroud, mainly for food production, but also for fibre production, possibly.
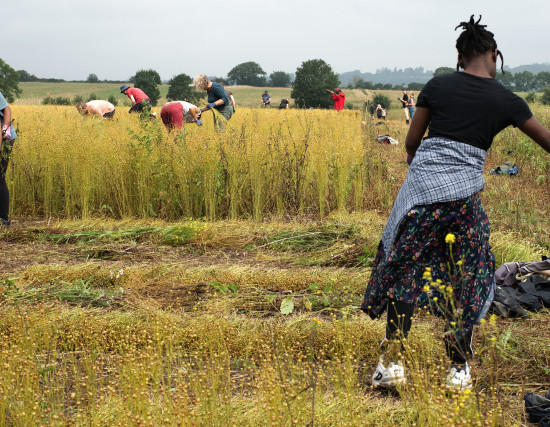
Rosie: flax is a great dual crop, because you can eat the seeds. Lots of potential for side projects like linseed oil.
Dave: is it the same plant that produces seeds and fibre?
Rosie: yes. There are 2 varieties, but they’re closely related. The linseed variety is shorter and produces more flowers. The fibre variety is taller with fewer flowers / seeds. It’s putting more of its energy into producing fibre. But you can harvest and eat the seeds from the fibre variety, and you can harvest the straw from the seed variety – you just get less of it, because the stalks are shorter.
Dave: flax has the blue flowers, doesn’t it? When you see blue fields, it’s flax?
Rosie: yes. Most of the blue fields nowadays are more likely to be for seed. But there are a few projects springing up around fibre growing.
Dave: I’m wondering what would actually be commoned in a textile commons. The machinery? The land for growing? The knowledge? The workshops / little factories? The shops? The finished linen? All of the above?
Rosie: maybe all of the above. We’re hoping that our mill / processing facility will be a co-operative. Something that’s part of the community. And definitely the knowledge of how to build and use the machines. We’re keen to share that as far and wide as possible.
Dave: it could provide quite a lot of jobs as well, couldn’t it?
Rosie: definitely. It’s a huge project if you think in terms of the UK producing all of its own fabric.
Dave: yes, I was going to ask about your ambitions, and what kind of a scale you think it could get to.
Nick: for me, Fantasy Fibre Mill plays lots of roles in this. One of the roles is a yarn / textile producer. In trying to achieve that, we’ve taken a massive detour. Now I’d like to see us as a provider of infrastructure that other people can tap into and set up in their towns. When you ask ‘how can this be commoned, I’d almost like to reinterpret that as ‘what’s the business model – how do we make this work financially for everyone involved?’ People will own and be able to fix their own machines. I see us as being textile producers, but also enablers for this infrastructure to emerge. That’s not just relevant to Britain, but also to other countries across Europe. Through the Fibreshed network we’ve got a lot of interest from people in Spain, Germany, Denmark who also want the infrastructure to produce yarn. The concept can be applied to other fibres too. It’s easier to process wool, for example.
Dave: when it comes to the future-use vouchers idea to get investment, I wonder whether you’d issue vouchers for the finished linen.
Rosie: sorry, I’m not familiar with that. What’s a future-use voucher?
Dave: I use the example of energy commons – it seems to be the easiest way to explain it. Imagine you have an energy commons group, who want to put up a wind turbine, but they don’t have the money to do it. At the moment, they’d have to go to the bank and get into debt, or sell equity in the business. But with either of those routes, it’s not going to be commons for very long. A senior research fellow at UCL came up with the idea of issuing vouchers, that will be redeemed for the energy that will be generated, once the wind turbine is built. That’s how they get the money to put up the turbine. The vouchers are denominated in kWh, not £. That makes them inflation-proof, because a kWh is the same in 20 years time as it is now. A £ isn’t. In your case, the vouchers might be denominated in lengths of yarn or square metres of cloth, I don’t know.
Nick: they could even be clothing, depending on how far along the production process you want to go. I love this idea – I definitely see it as applicable to what we’re doing. At the moment, the big difference between us and an energy commons is that if you buy a wind turbine, you know that’s going to produce x amount of electricity. There isn’t so much risk. There’s a high risk in our technology because we can’t tell you that our machines can produce x amount of yarn or fabric. Hopefully in a couple of years we will.
Rosie: I’d heard of that, I just didn’t associate it with future-use vouchers.
Dave: the fancy name is use-credit obligations, but we don’t tend to use that, as it’s too much of a mouthful.
Rosie: once we’ve made yarn that we’re pleased with the quality of, that will be the kick-off point. We’ve talked with lots of people who are excited about it, but want to see a yarn sample. But we’re not quite there yet.
Dave: you could produce some sort of a prospectus, and instead of vouchers for finished goods, there could be a series of agreements to buy vouchers for yarn or textiles further down the line. You’d be asking investors how much they’d be prepared to pay for vouchers in the future, when certain quantity and quality milestones have been met.
Nick: so if you bought vouchers earlier it would be higher risk, so you’d get more for your money, and it’s worth doing because the value of the vouchers increase later on. There are ways to incentivise people to take on the extra risk.
Dave: yes, the earlier investors get in, you’d have to provide bigger discounts, because the risk would be greater.
Rosie: at the moment, we’re lucky to have grant funding, but we’ll be looking at those ideas soon.
Dave: where do you get your seeds from?
Rosie: big question. This year we’re using Elsoms to import seeds. We’re using 3 varieties, and we’re going to grow them and trial them by keeping track of height / weight etc.
Dave: where are they imported from?
Rosie: the Netherlands. There are a few big seed producers in Europe. Nick’s been working on another project with Fibreshed Scotland, to create a UK source of seeds that are unpatented. At the moment, all the seeds we can get our hands on are patented, which means that you can’t save the seeds. You have to re-buy them every year.
Nick: there’s a company in Oregon doing similar things to us, called Fibrevolution. They’re a few years ahead of us, and are expert seed breeders. They’re interested in unpatented seeds, and are more in the commoning spirit. We’re hoping to import some seeds from them, that would be unpatented, and we’d be able to grow our own from. But there’s lots of paperwork. But we’re very keen to make it happen.
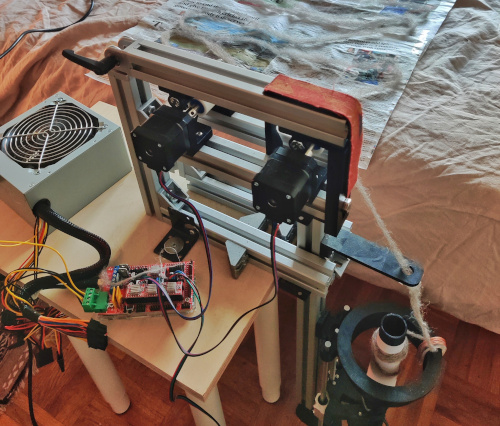
Dave: what other barriers do you face, and what needs to happen to remove them or get round them?
Rosie: to import seeds we have to register officially as seed importers with the UK government, which is a lot of bureaucracy; and then we have to get the seeds certified to show that they don’t have any diseases. On a bigger level, it would be great if large companies would stop patenting their seeds. We can’t save the seed – the big corps want it to be that way, otherwise their customers would just be one-time customers, and they don’t want that. But we’re hoping to change that, and allow UK growers to save their own seed in future. It’s going to be hard work, but it’s a one-off, then things will be much easier.
Dave: are you connected with any other like-minded organisations? I think you’ve been working with Fibreshed haven’t you? How do you collaborate?
Nick: Fibreshed is a fantastic network. It started in the US, but they have affiliates all over the world. Through them we’ve met some great people. I’d like to shout out Jordan Masters at the University of West Virginia, who we connected with a few years ago. He’s been amazing, looking at the kind of machinery we need. In our Discord group we’ve got a community of people working on these machines. He’s already producing wool yarn with the machinery. In the UK there’s various Fibreshed organisations, and we’ve also been working closely with the Soil Association.
Dave: so the textiles you’ll be producing will not only be local and commons, but also organic?
Rosie: definitely. I’m really keen that everything we produce will be organic and regenerative. I’m doing a PhD, working on a life-cycle assessment of a linen garment from planting, growing and harvesting, through all the processes to composting at the end of its life. If it’s all natural materials, including natural dyes, rather than sitting in landfill, it will decompose and put all its nutrients back into the soil. We can compare this to the effect of the current textile industry.
Dave: what about price? The big corporations who exploit cheap labour, damage the environment, don’t pay taxes like small businesses do, and have economies of scale, will undercut you on price. What can we do about that?
Nick: first, we’re not aiming to compete with Primark et al on price. There’s a discussion around the cost of clothing – some say that you can’t expect people to pay high prices for clothing. But we need to separate consumer behaviour from the poverty question. Some people can barely afford clothing, but that’s a different discussion from the one about people who can afford clothing, but who prefer to spend their money on lots of cheap, poor-quality items instead of fewer good-quality, but higher-priced items. We’d like to persuade those people that the latter option is better.
Rosie: also, if you don’t think about prices per item, but price per wear, it makes more sense. If you buy something high-quality you can keep it for decades. I still have clothes that were my grandmas, but I still get good wear out of them, because they were such good quality, whereas cheap clothes can work out much more expensive per wear, because they wear out so quickly. And this is before we even take environmental degradation and health into consideration.
Nick: but the problem with this discussion at the moment is that if people right now spend more money on clothes, they’re often not getting better quality, or better supply chains, because the current fashion industry is about designing clothes that then get made via global supply chains. But in our new localised model, where you know that your clothes are being made in a local factory that you can visit, that changes your relationship with clothes. Plus you can potentially get a job there. Then we’re talking about something very different. But right now, it’s a bit of an illusion that there’s a better option. There are slightly better options, but they’re not that much better really.
Rosie: the other model I’m interested in is community-supported agriculture, where people pay up front for veg.
Dave: yes, the CSA model is the future-use voucher model, really.
Rosie: exactly – and the CSA farms I’ve visited have a sliding scale, because they don’t want to price out local people who can’t afford locally-produced organic veg. And as Nick said, people experiencing poverty are not the ones causing the problems of overconsumption.
Dave: because we’re looking at a commons approach, we can find ways together to help people in communities who are having difficulties.
Rosie: also, we’re not trying to solve all problems ourselves. There will be lots of little solutions. But it’s important to keep wearing and repairing the clothes you have in your wardrobe right now (assuming they’re high enough quality to be repaired).
Dave: how do we replicate what you’re doing in as many communities as possible? You say you’re producing guides, instruction manuals and toolkits etc? How’s that going?
Rosie: it’s going well. We’re already sharing plans for machinery with another group, to see if the instructions are easy to follow. When we’re happy that the machines and the instructions work, then we’ll do a big publicity announcement.
Dave: we’ll help with that.
Nick: some of the instructions are available already on GitHub. Our cutting edge stuff isn’t online yet, but we have some of the more tested materials on GitHub. Once the dust has settled, we’ll put some effort into making it all look nicer, and be more organised about it. At the moment we’re full steam ahead getting everything working.
Dave: how can people help you? How can they get involved?
Rosie: if people want to build a machine, they can join our Discord server / online forum. People can see what we’re up to on the website, join the mailing list, and we’re hoping to have an open day soon. And they can buy yarn when it’s available.
Dave: let’s stay in touch – we’ll interview you again to see how you’re progressing. It’s very exciting.
Nick: yes, and we’re excited to be part of this commons movement.
Dave: OK, I’ll post this video, with a transcript, and I’ll show it to commons specialists, and interview them and post that too, so you can see it, then hopefully bring you all together for a discussion, which we’ll post too.
Rosie & Nick: thanks very much Dave
Highlights
- Fantasy Fibre Mill want to resurrect the flax / linen industry in the UK – as a commons. We can help bring together flax specialists and commons specialists to work out how to do that.
- They’re building the flax-processing machinery from scratch, from designs in Victorian textbooks.
- They’re building (open-sourced) farm-scale equipment so that farmers can process their own crop. They don’t want to become a massive centralised factory. They foresee lots of little hubs all over the place, that can process everybody’s local fibre. We don’t want to replicate the problems of the current system.
Leave a Reply